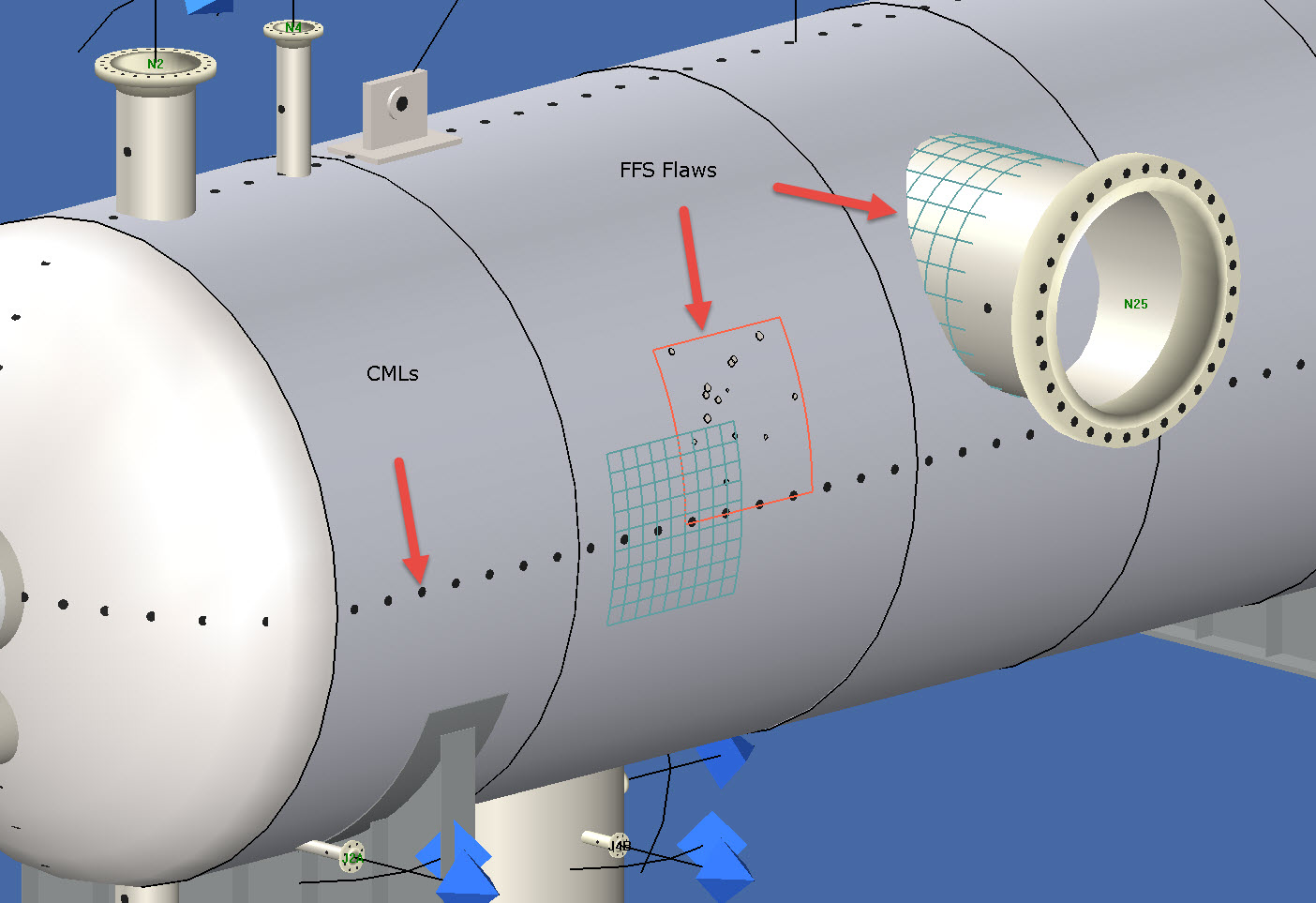
Decoding API 510 Inspection: Ensuring Integrity of Pressure Vessels
Do you know how pressure vessels are inspected to ensure their integrity?
In this guide, we will decode the API 510 Inspection process. This inspection is crucial for maintaining the safety and reliability of pressure vessels in various industries. By following the guidelines set by the American Petroleum Institute (API), you can identify potential issues before they become major problems.
We will explore the key components of API 510 Inspection, the benefits of regular inspections, and the common issues that can be detected. Whether you are involved in the design, fabrication, or operation of pressure vessels, understanding API 510 Inspection is essential for ensuring their long-term performance and preventing costly accidents.
Key Takeaways
– API 510 Inspection is essential for regulatory compliance and ensures the integrity of pressure vessels.
– Industries like oil and gas, chemical, and power generation rely on API 510 Inspection for safe and efficient functioning of pressure vessels.
– Adhering to API 510 Inspection helps avoid costly fines and reputational damage.
– Early detection of potential issues through API 510 Inspection increases safety, extends equipment lifespan, and enhances operational efficiency.
Importance of API 510 Inspection
To understand the importance of API 510 Inspection, you must recognize how it ensures the integrity of pressure vessels. This certification is essential for regulatory compliance and guarantees that pressure vessels are functioning safely and efficiently.
In industries where pressure vessels are used, such as oil and gas, chemical, and power generation, ensuring their integrity is paramount to prevent accidents, leaks, and catastrophic failures. API 510 Inspection plays a crucial role in achieving this by evaluating the structural integrity of pressure vessels, identifying potential defects or weaknesses, and recommending necessary repairs or replacements.
It ensures that pressure vessels meet the required standards and are in compliance with industry regulations. By adhering to API 510 Inspection, companies can avoid costly fines, reputational damage, and, most importantly, protect the safety of their employees and the public.
Now, let’s delve into the key components of API 510 Inspection.
Key Components of API 510 Inspection
The key components of API 510 Inspection include:
– Evaluation of pressure vessel structural integrity
– Identification of defects or weaknesses
– Recommendations for repairs or replacements
To ensure the structural integrity of pressure vessels, API 510 Inspection evaluates whether the vessel design meets the necessary design requirements. This involves examining the materials used, weld quality, and the overall construction of the vessel.
The inspection procedures involve a thorough examination of the vessel, including visual inspections, non-destructive testing, and pressure testing. These procedures are designed to identify any defects or weaknesses that may compromise the safety and performance of the vessel.
Based on the findings, the API 510 Inspection provides recommendations for repairs or replacements to rectify any issues and ensure the continued integrity of the pressure vessel.
Benefits of Regular API 510 Inspections
Regular API 510 inspections offer numerous benefits, ensuring the cost effectiveness and regulatory compliance of pressure vessels. Here are five key advantages of conducting these inspections:
– Early detection of potential issues: Regular inspections help identify and address problems at an early stage, preventing major failures and costly repairs.
– Increased safety: By identifying and rectifying any structural or operational deficiencies, inspections enhance the safety of pressure vessels, protecting personnel and the environment.
– Extended equipment lifespan: Timely maintenance and repairs identified through inspections can extend the lifespan of pressure vessels, maximizing their value and reducing the need for replacement.
– Compliance with industry standards: API 510 inspections ensure that pressure vessels meet the stringent requirements set forth by regulatory bodies, minimizing the risk of penalties and legal consequences.
– Enhanced operational efficiency: Inspections optimize the performance of pressure vessels, improving their reliability and efficiency, leading to increased productivity and reduced downtime.
Regular API 510 inspections play a vital role in maintaining the integrity and functionality of pressure vessels. In the next section, we’ll discuss the common issues detected by these inspections.
Common Issues Detected by API 510 Inspection
During API 510 inspections, you may encounter several common issues that can impact the integrity of pressure vessels. One such issue is corrosion, which can weaken the vessel and lead to leaks or failure. Inspectors should carefully evaluate the condition of the vessel’s internal and external surfaces to identify any signs of corrosion.
Another common issue is improper maintenance practices, which can include inadequate cleaning, lack of regular inspections, and failure to address identified issues in a timely manner. These practices can contribute to the deterioration of pressure vessels and compromise their safety.
To mitigate these issues, it’s crucial to implement effective corrosion prevention measures, such as proper coating systems and cathodic protection. Additionally, regular inspections and proactive maintenance practices are essential to ensure the long-term integrity of pressure vessels.
Implementing API 510 Inspection in Industry
To effectively implement API 510 inspection in your industry, focus on proper training and adherence to industry standards. Consider the following steps for a cost-effective implementation and to overcome compliance challenges:
– Conduct thorough training programs for inspectors to ensure they possess the necessary knowledge and skills.
– Develop and maintain a comprehensive inspection plan that addresses all relevant aspects of API 510.
– Regularly review and update procedures to ensure compliance with the latest industry standards and regulations.
– Implement a robust documentation system to track inspections, findings, and corrective actions.
– Foster a culture of safety and continuous improvement by promoting open communication and feedback.
Conclusion
In conclusion, the API 510 inspection plays a vital role in ensuring the integrity and safety of pressure vessels. By conducting regular inspections, industries can identify and address potential issues before they escalate, preventing costly downtime and accidents.
From detecting corrosion and leaks to assessing structural integrity, API 510 inspections provide a comprehensive evaluation of pressure vessels.
So, can industries afford to neglect this crucial inspection?